اثرات اجرای TPM روی بهره وری کلی تجهیزات(OEE)
واژه های کلیدی:
بهره وری کلی تجهیزاتOEE، نگهداری و تعمیرات بهره ور گرایانه TPM ، شش ضایعه بزرگ، قابلیت دسترس پذیری، بازده اجرایی، میزان کیفیت محصولات.
چکیده:
درابتدا چکیده کوتاهی از TPM و تاریخچه آن و دلایل رویکرد صنایع به آنرا می خوانیم و سپس جایگاه بهره وری کلی تجهیزات (OEE ) را به عنوان یکی از ستونهای اجرای TPM مورد اشاره قرار میدهم همچنین در این مقاله سعی خواهد شد تا با تعریف کامل علمی ، همراه با ارایه فرمولهای مربوطه برای OEE ،نقش OEE را بعنوان یک شاخص در تعیین موفقیت اجرای TPM مورد بررسی قرار دهم. بعد از ارائه فرمول با دو مثال جالب آنرا بهتر نشان خواهیم داد و شرایط واقعی محاسبه آنرا خواهیم دید.
همانطور که میدانیم پس از اجرای TPM باید میزان موفقیت اجرای آنرا مورد مطالعه قرار دهیم. وجود یک Benchmark در این موارد میتواند کمک مناسبی باشد ولیکن مشکلات فراوانی دارد که در این مقاله این مشکلات بیان خواهد شد.
نیاز به یک شاخص استاندارد که مورد قبول همگان نیز باشد موجب استفاده از ابزار OEE شده است.با این ابزار میتوان تاثیر اجرای TPM در کاهش شش ضایعه بزرگ (که یکی از مهمترین اهداف TPM است ) را در سطح کارخانه به خوبی دیده و موارد اشکال آنرا مورد مطالعه قرار دهیم. این امر کار مدیریت ارشد و میانی را درتصمیم گیری تسهیل میکند.
بعلاوه این شاخص درصدهای استاندارد را بعد از اجرای TPM به ماارائه داده تا در تعیین جایگاهمان در میان دیگر شرکتها به ویژه آنهایی که TPM را اجرا کرده اند کمک میکند.
در خاتمه چگونگی تاثیر اجرای TPM روی افزایش OEE مورد بررسی قرار خواهد گرفت.
مقدمه:
در گذر زمان تغییرات وسیعی در روشهای تولیدات صنعتی بوجود آمد که اهم آنرا میتوان به سه روش مهم اشاره کرد که در زیر آمده است
mass production
tail production
lean production
اگر چه در اینجا مجال کافی برای بحث راجع به کلیه این مباحث نیست اما برای آگاهی از مبانی ریشه ای ایجاد سیستم TPM شناخت مختصری از این روشهای تولید جالب و شاید الزامی باشد.
در روش اول که روشی آمریکایی است سرمایه اولیه فراوانی برای تولید موجود است و از مهمترین شاخصه های آن نبود تنوع کافی محصولات و در عوض اعطائ تسهیلات فراوان برای مشتری و وادار کردن آنها به خرید و … است. اما بعد از جنگ جهانی دوم و هنگامی که دیگر کشورها از جمله ژاپن در فکر تولید و رقابت با امریکا بر آمد آنها با مشکل کمبود سرمایه مواجه بودند ولذا نمیتوانستند که از روش تولید ناب استفاده کنند و مجبور به اعمال تغییرات جدی در روش تولیدی خود شدند و آن حرکت به سمت تولید ناب lean production بود مبنای کار این روش تولید بر اساس خواسته مشتری با حداکثر کیفیت و حداقل زمان انتظار مشتری برای محصول با کمترین ضایعات ممکن بود برای رسیدن به این هدف مهندسان ژاپنی میبایست خط تولیدی کاملا تغییر پذیر flexible طراحی می کردند تا زمان تنظیمات و تغییرات برای تولید محصول جدید نزدیک به صفر باشد تا بتوانند تنوع فراوان محصول بر اساس سلیقه مشتری در بازار تولید کنند برای رسیدن به این اهداف و دیگر اهداف تولید ناب که در اینجا ذکر نشد تولید کنندگان را بر آن داشت تا با استفاده از ابزارهایی به این هدف برسند که این ابزارها شامل Just in time, Automation و Total productive maintenance می باشد.
پس میتوان دید که اساس و منشا TPM را می توان در تولید ناب دانست و آنرا به عنوان ابزاری در جهت رسیدن به اهداف کلی تولید ناب قلمداد کرد.
تاریخچه مختصری از TPM :
TPM یک ابداع از مهندسان ژاپن است اولین بار نگهداری و تعمیرات پیشگیرانه (preventive maintenance) در سال ۱۹۵۱ اززادگاهش ایالات متحده به ژاپن آورده شد و اولین بار در شرکت Nippondenso در سال ۱۹۶۰ اجرا شد اصول سیستم PM بر این پایه بود که گروه اوپراتورها تنها وظیفه تولید درست را بر عهده داشتند و گروه نگهداری و تعمیرات عهده دار هر گونه نظارت وتعمیرات در سیستم بودندو شعار آنها این بود که “من اپراتور هستم و تو تعمیرات را انجام بده”. با آمدن اتوماسیون در صنعت نیاز به تغییر در روشهای قدیمی نگهداری و تعمیرات بیشتر احساس شد زیرا اساسا کار نگهداری و تعمیرات را نمیتوان بصورت اتوماسیون نمود چون در صورت خرابی باید یک نیروی انسانی کار تعمیر آنرا بر عهده گیرد حتی برای پیشرفته ترین سیستمها نیز این امر صادق است. مثال این امر را می توان در شاتلها و ماهواره ها ی امروزی دید که گر چه از پیشرفته ترین سیستم های خودکار برخوردارند اما قادر به تعمیر خود بدون کمک انسان نیستند و این بزرگترین معضل اتوماسیون در صنعت امروزی است که توضیح بیشتر آن در این مقاله نمی گنجد. در نتیجه راه حلی که مدیران شرکتNippondenso به آن رسیدند استفاده از سیستم نگهداری و تعمیرات تجهیزات بوسیله اوپراتور بود این شرکت با اضافه کردن Autonomous Maintenance به سیستم PM و در نهایت با اعمال تغییرات دیگر به TPM منجر گردید. بدین ترتیب این شرکت که یکی از شرکتهای تولید قطعات TOYOTA بود به عنوان اولین کمپانی دارنده گواهینامه TPM در ژاپن ودر جهان بود.
TPM چیست؟
سیستم تعمیر و نگهداری کلی بهره ورگرایانه (Total productive maintenance) سیستمی است بر گرفته از تعمیرات پیشگرانه آمریکایی که در ژاپن با فرهنگ و مقتضیات آن کامل شده است و به جهان عرضه شده به گونه ای که هم اکنون بسیاری از شرکتهای اروپایی و حتی آمریکایی از آن استفاده میکنند هدف برنامه TPM افزایش تولید و کاهش ضایعات و توقفات و همزمان بهبود شرایط اخلاقی و رضایتمندی از کار در پرسنل است.
تعریف:
سیستم تعمیر و نگهداری کلی بهره ورگرایانه سیستمی است که در آن همه پرسنل از مدیریت گرفته تا پایین ترین سطح را در کار تولید درگیر میکند به گونه ای که آنها را در تیمهای کوچک دسته بندی کرده و یک استقلال کاری به آنها داده تا حتی بتوانند در بعضی موارد لازم تغییراتی در طراحی نیز بدهند.
اهداف:
رسیدن به تعداد خرابی صفر (zero defect)
تعداد توقفات و تصادفات صفر (zero breakdown and accident) در همه زمینها در یک سازمان.
درگیر کردن همه پرسنل در هر سطحی در کار و نگهداری
ایجاد تیمهایی برای کاهش خرابی و تعمیر و نگهداری مستقل
مزایای مستقیم:
۱- افزایش بهره وری
۲- افزایش OEE به میزان حداقل ۸۵%
۲- برطرف کردن شکایات مشتریان
۳- کاهش هزینه تولید تا ۳۰%
۴- راضی کردن نیازهای مشتریان تا ۱۰۰%
۵- کاهش تصادفات
۶- کاهش مقادیر آلودگی
ستونهای :TPM
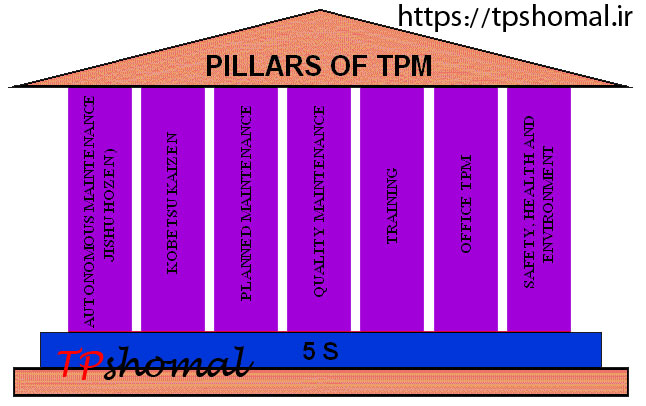
بهره وری کلی تجهیزات (Overall Equipment Effectiveness (OEE :
تا اینجا خلاصه ای از TPMو مزایا و اهداف آنرا بصورت خیلی مختصر بیان نمودم ولیکن راجع به اجرا و نحوه اجرای آن چیزی بیان نگردید زیرا ۱۲ مرحله اجرای آن به بحث زیادی نیاز دارد زیرا بعضی از مراحل آن نیز خود به چند زیر مرحله تقسیم می شوند. زمان اجرای یک برنامه TPM در صنعت ژاپن که از نظم و مقررات مثال زدنی برخوردار است سه سال پیش بینی شده است که مسلما در کشور ما این زمان افزایش مییابد.
حال میخواهیم جایگاه بهره وری کلی تجهیزات را در اجرای TPM ببینیم. برای کارخانه ای که TPM را به اجرا در میاورد این نکته مهم است که جایگاه خود را در مقایسه با دیگر رقبایی که آنرا اجرا کرده اند ببیند برای این امر نیاز به یک شاخص استانداردی است که به صورت عددی این امر را نشان دهد. و در ضمن میزان موفقیت ما را در طی اجرای کار بر آورد کند و بصورت اماری عددی در گزارشات برای متقاعد کردن مدیریت ارشد( این امر برای ادامه کار بسیار مهم است) بکار رود. اگر چه این امر به ظاهر راحت مینماید اما در اجرا مشکلات فراوانی به همراه دارد و برای کارخانجاتی که سیستم PM را هنوز به اجرا نگذاشته اند این کار به مراتب سخت تر است. زیرا ثبت رکورد واندازه گیری آن در طی پریود طولانی به یک سازماندهی دقیق، بدون تغییر و آگاهی نیاز دارد.
در ابتدی اجرای TPM باید مقدار OEE تجهیزات را اندازه بگیری کنیم. شاید این سوال پیش آید که برای اینکار نیاز به زمان و دقت زیادی برای جمع آوری اطلاعات و رکورد گیری از آنهاست و این امر به صرفه نیست. برای رفع این معضل باید به چند نکته توجه کرد.
- در بعضی موارد میتوان برای محاسبه OEE بجای اندازه گیری روی تک تک تجهیزات از مجموعه ای از تجهیزات که هدف و عملکردی همراستا دارند استفاده کرد.
- طبق اصلی که به نمودار پارتو که در ایران به هشتاد، بیست و یا هفتاد ،سی معروف است بیان میدارد که هفتاد(هشتاد) درصد خرابی ها در مجموعه بخاطرسی( بیست) درصد تجهیزات است. طبق این اصل ما میتوانیم کارمان را روی آن بیست درصد تجهیزات متمرکز کنیم.
سوال دومی که ممکن است بیان شود استفاده کردن از روش Bench mark که روشی شناخته شده در ر اه یافتن جایگاه و میزان موفقیت شرکت است بجای این روش است.
جواب به این سوال چندان سخت نیست زیرا اساسا روش فوق الذکر مشکلاتی دارد که چند نمونه از آنها در زیر آمده است:
- با روش Bench mark نمی توان اطلاعات درستی از دیگر شرکتهای رقیب پیدا کرد زیرا معمولا چنین شرکتهایی اطلاعات خود را به آسانی در اختیار رقبا قرار نمیدهند.
- شرایط شرکتهای مشابه اما در جاهای مختلف هیچگاه یکسان نیست و مسایلی مانند آب و هوا ،فرهنگ ، عمر کارخانه و غیره متفاوت است. ولذا مقایسه نسبت به یک مبدا کمی نادرست است.
دلایل دیگری هم موجود است که به بحث بیشتری نیاز دارد. اما در روش OEE مسائل وابسته به شرایط نیستند وبر اساس پارامترهای ثابت زمان و ظرفیت تولید و… میباشد که برای همه یکسان میباشند ( در قسمت فرمول بطور کامل بحث خواهد شد.).
برای رسیدن به اهداف اصلی TPM و خصوصا zero defect و zero breakdown و zero accident نیاز به حذف ۶ big losses میباشیم. در ابتدای امر باید این شش ضایعه بزرگ را بشناسیم.
شش ضایعه بزرگ:
۱- Breakdowns
۲- Setup and adjustment
۱ , ۲ -> Down time
۳- Idling and minor stoppages
۴- Reduce speed
۳ , ۴ -> Speed losses
۵- Process defect
۶- Reduce yield
۵ , ۶ -> Defects
ادامه دارد